The anode cages enable to use bulk anodes of various shapes (spherical, hemispherical); the active surface of bulk anodes may be much larger than that of plate anodes.
The formation of significant amounts of anode wastes at the electroplating production facility is caused by the incomplete immersion of anodes in the tank, as well as their uneven dissolution. Due to the impossibility of secondary use of plate anodes, they must be recovered in a timely manner and sent for recycling. The use of the anode cages makes it possible, in particular, to simplify the process of collecting anode fragments 25 to 50 mm in size. Owing to such a device, it is possible to reduce the production costs and make sure the re-use of wastes.
The cage is hanged on the anode rod using two hooks made of titanium or another chemically resistant alloy. The hooks are made of a metal strip, the narrow edge of which is turned towards the rod for hanging. Owing to this technological solution, the hook cools faster, and its design creates an increased pressure in the contact area, which can be reinforced additionally with a copper or nickel pad.
The formation of significant amounts of anode wastes at the electroplating production facility is caused by the incomplete immersion of anodes in the tank, as well as their uneven dissolution. Due to the impossibility of secondary use of plate anodes, they must be recovered in a timely manner and sent for recycling. The use of the anode cages makes it possible, in particular, to simplify the process of collecting anode fragments 25 to 50 mm in size. Owing to such a device, it is possible to reduce the production costs and make sure the re-use of wastes.
Design specific features and operating conditions of the anode cages
The anode cages are made with a rectangular cross-section, 50 to 100 mm wide and 100 to 300 mm long. The height of the cage is calculated depending on the size of the anode used. The end walls and bottom are made of a solid sheet, the front wall is made of mesh or horizontal rods with a pitch of 20 mm. The bottom of the cage has sides 20 to 30 mm high. It is important that the upper edge of the cage is located 5 to 7 cm above the electrolyte surface, which will allow to load the cage without removing it from the tank.The cage is hanged on the anode rod using two hooks made of titanium or another chemically resistant alloy. The hooks are made of a metal strip, the narrow edge of which is turned towards the rod for hanging. Owing to this technological solution, the hook cools faster, and its design creates an increased pressure in the contact area, which can be reinforced additionally with a copper or nickel pad.
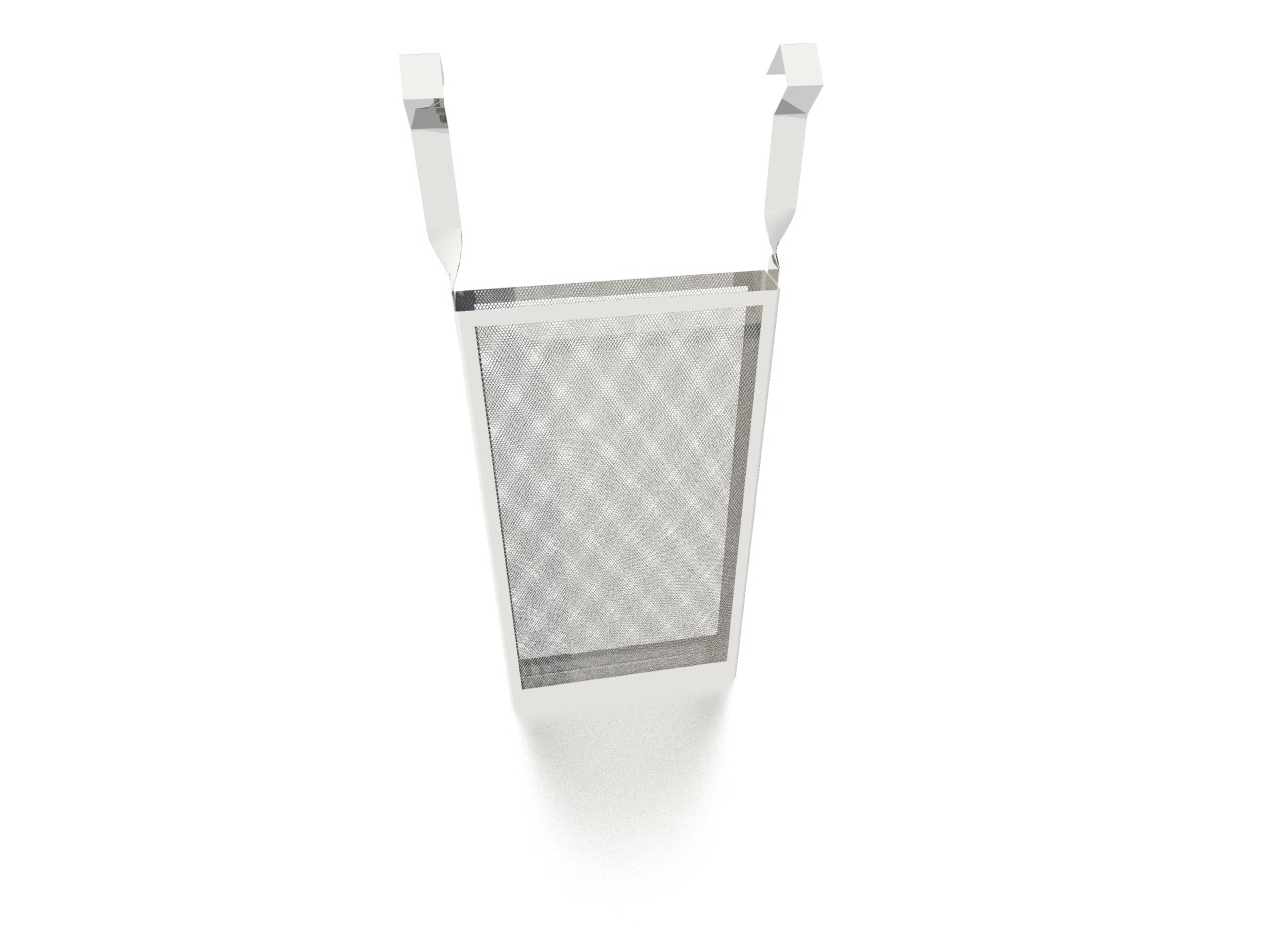
Overview 360°
When calculating the cross-section of the current-carrying titanium parts of the cage, the ratio of 1A per sq. mm is used, and for the elements, immersed in the electrolyte, the ratio of up to 5 A per sq. mm is used. When the tank is fully loaded, the hooks lose not more than 1% of electricity, which reduces the energy intensity of the equipment and makes it possible to expect the reduced prime cost of products.
Important: the use of the titanium anode cages implies their filling with anode cuttings above the edges of parts to be treated. Otherwise, there is a risk of starting the titanium corrosion process due to an increase in the stress level on the cage wall opposite the protruding point of a part. If current is applied to the empty cage, its potential rises sharply and reaches the limits of the anodic oxidation potential. As a result, the film, formed on the metal surface, will become much thicker and lose some of its conductive properties. And, in order to preserve the cage, it will be necessary to etch it to restore full contact with the anode waste, placed inside it. If there is no current, the cage may be stored in the idle tank for a long time. To prevent the destruction of the metal due to prolonged contact with reagents under the influence of electric current, the cage is covered with a cover similar to the one used to protect the anode.
Specific features and benefits of the titanium anode cages
The titanium cages are considered to be the best solution, significantly superior to metal and polymer structures in terms of their package of advantages. The film, formed on the surface of titanium due to contact with oxygen or other oxidants, has a relatively low impedance, which is minimized in areas with increased specific pressure. As a result, to overcome the film resistance and to supply current to the working solution, it is necessary to increase the amount of electricity by only 0.1 V, which is five times less than the permissible limit, taking into consideration the possibility of maintaining the initial prime cost of products and the nominal energy intensity of the unit. Also, among the advantages of the titanium cages, which led to the increased demand for the products from companies, having electroplating production facilities, are a long service life, economic feasibility and increased chemical resistance.Important: the use of the titanium anode cages implies their filling with anode cuttings above the edges of parts to be treated. Otherwise, there is a risk of starting the titanium corrosion process due to an increase in the stress level on the cage wall opposite the protruding point of a part. If current is applied to the empty cage, its potential rises sharply and reaches the limits of the anodic oxidation potential. As a result, the film, formed on the metal surface, will become much thicker and lose some of its conductive properties. And, in order to preserve the cage, it will be necessary to etch it to restore full contact with the anode waste, placed inside it. If there is no current, the cage may be stored in the idle tank for a long time. To prevent the destruction of the metal due to prolonged contact with reagents under the influence of electric current, the cage is covered with a cover similar to the one used to protect the anode.